What are the Differences Between LNG Cylinders and LPG Cylinders?
Release time: 2025-07-08
In the vast field of clean energy applications, both liquefied natural gas (LNG) and liquefied petroleum gas (LPG) serve as important alternative fuels. They both require specialized storage containers to ensure safe and efficient use. HSDP, a leading manufacturer in the field of specialized pressure vessels since 1997, has extensive technical expertise in CNG/LNG cylinders, LPG containers, and other related products. Below, we will provide an in-depth analysis of the differences between LNG cylinders and LPG cylinders.
Core Differences Between LNG and LPG Cylinders
Storage Substance
LNG Cylinders: Store liquefied natural gas, which is primarily composed of methane. It is liquefied by deep cooling to about -162°C under normal pressure. LNG is about 1/600 the volume of natural gas in its gaseous state, making it more convenient for storage and transportation.
LPG Cylinders: Store liquefied petroleum gas, which is primarily composed of propane and butane (or a mixture of both). It is liquefied at normal temperatures by applying a certain amount of pressure (usually in the range of several bar to over ten bar). LPG is about 1/250 the volume of gaseous petroleum gas.
Storage State and Core Parameter Differences
LNG Cylinders:
Low-Temperature, Normal Pressure Storage: The key challenge is maintaining extremely low temperatures (close to -162°C) to keep it in liquid form. The operating pressure is relatively low (much lower than LPG cylinders).
“Insulation” is Key: It is crucial to minimize external heat input to prevent LNG from vaporizing too quickly and causing pressure buildup.
LPG Cylinders:
Normal Temperature, High-Pressure Storage: The core challenge here is withstanding higher internal pressures. The temperature fluctuates within the range of the ambient temperature.
“Pressure Resistance” is Key: The structure must be strong enough to safely contain the saturated vapor pressure generated by liquefied gas at ambient temperature.
Structural and Material Differences
LNG Cylinders (commonly used in vehicle vacuum insulated cylinders):
- Double-Layer Vacuum Insulated Structure: Similar to a “thermos bottle.” The inner tank holds LNG, and the outer shell encases the inner tank. The gap between the two is evacuated to high vacuum and filled with multiple layers of insulating material to create a super insulation layer, greatly reducing heat conduction and convection.
- Support System: The inner tank is fixed in place inside the outer shell by a special support structure made from low thermal conductivity materials. This system ensures both strength and minimal heat transfer.
- Valves and Pipelines: Special low-temperature valves and pipelines are used to ensure reliable operation at extremely low temperatures.
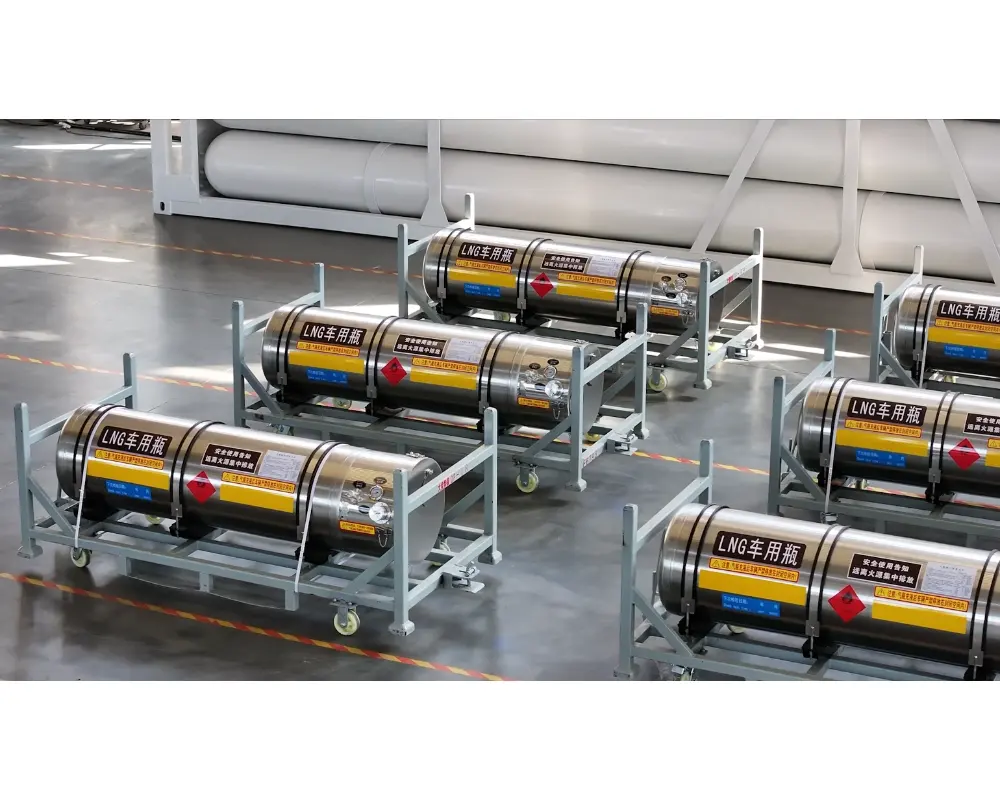
LPG Cylinders (commonly used in household LPG cylinders):
- Single-Layer Thick-Walled Structure: Typically a single-layer pressure vessel wall, made from high-strength steel or advanced composite materials. The wall thickness is designed to meet high-pressure requirements.
- Relatively Simple: The structure is relatively simple compared to LNG cylinders, not requiring complex vacuum layers or super insulation. The primary focus is on material strength, toughness, and fatigue resistance.
- Safety Attachments: Must be equipped with safety valves, level gauges, emergency shutoff valves, and other safety devices.
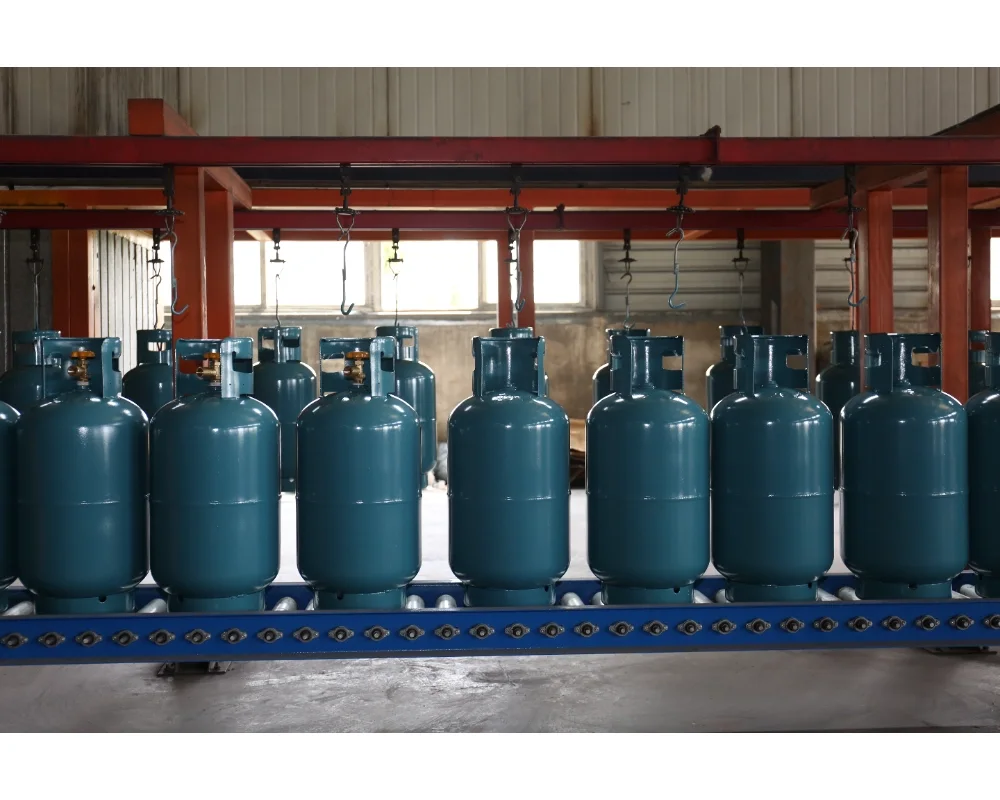
Differences in Application Scenarios
LNG Cylinders are primarily used for:
- Heavy-duty long-distance transportation vehicles as fuel.
- Vessels (LNG-fueled ships).
- Mobile refueling trucks.
- Areas with high requirements for driving range and a relatively well-established LNG refueling infrastructure.
LPG Cylinders have a wide range of applications:
- Domestic/Commercial: Used as cooking fuel in households, restaurants (gas cylinders).
- Vehicle Use: In taxis, light commercial vehicles, and some private cars modified for LPG use (LPG refueling station networks are generally more established).
- Industry: Used for cutting, welding, heating, and other industrial processes.
- Agriculture: Used for greenhouse heating, grain drying, and more.
- Portable Equipment: For camping stoves, outdoor heaters, and more.
Safety Requirements
LNG Cylinders: Due to their low-temperature nature, LNG cylinders require special safety designs focusing on temperature control and leak prevention. Any change in temperature could cause LNG to convert from liquid to gas, generating significant pressure. Therefore, performance LNG cylinders often include complex safety devices such as temperature control valves and pressure regulating valves.
LPG Cylinders: The safety design of LPG cylinders primarily focuses on gas pressure and leak prevention. Since LPG is stored in liquid form at normal temperatures, the cylinder must withstand overpressure or leakage. Gas LPG cylinders typically feature pressure relief valves, safety valves, and venting devices to ensure safety in case of abnormal conditions.
As a leading manufacturer with nearly thirty years of experience, HSDP deeply understands the unique technical requirements of storage containers for LNG and LPG fuels. In the LNG field, HSDP has mastered advanced vacuum insulation technology, low-temperature material applications, and precision manufacturing processes, ensuring that its LNG cylinders offer exceptional insulation performance and long-term reliability. In the LPG field, HSDP relies on its strong pressure vessel design and manufacturing capabilities, rigorous quality control system, and deep understanding of safety regulations to produce high-quality, safe LPG containers for various applications.
Choosing the right cylinder essentially means selecting a safety solution that perfectly matches the fuel’s characteristics and application needs. Understanding the fundamental differences between LNG and LPG cylinders is the first step in making an informed decision.